関連するソリューション

セキュリティサービス

セキュリティ製品
IDアメリカ
ハムザ・アフメッド
オートメーションピラミッドとは
このフォーマットを下図のようにオートメーションピラミッドと呼ばれています。これが今までの業界標準であり、現在でも多くの製造業の工場で主要なアーキテクチャとして採用されています。このようなオートメーションピラミッドはOT(Operational Technology)とも呼ばれます。
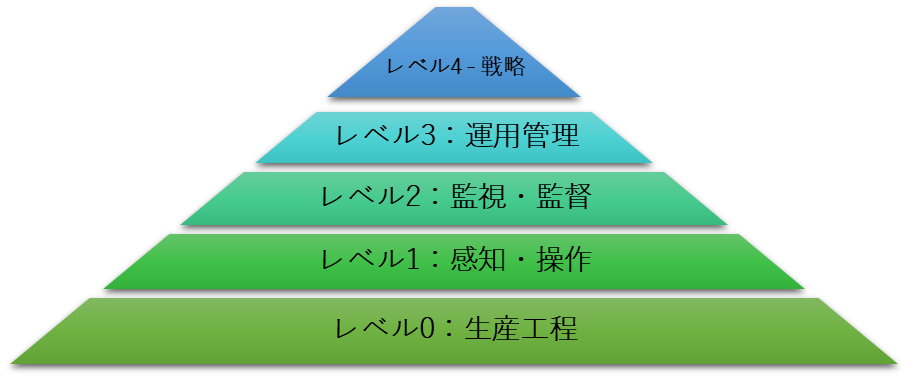
ピラミッド層
このレベルには、現場や生産現場にあるデバイス、アクチュエーター、センサーがあります。現場レベルとは、物理的な作業や監視が行われる生産現場のことで、機械を動かすための電気モーター、油圧・空圧アクチュエーター、特定の物質の動きを検出する近接スイッチ、類似のものを検出する光電スイッチなどが現場レベルの例として挙げられます。
レベル1:制御レベル / 感知・操作
このレベルでは、実際に物理的な作業を行うフィールドレベルのデバイスを制御・操作します。
- PLC(Programmable Logic Controller):組立ライン、機械、ロボット装置などプロセスの故障診断が必要な製造プロセスの制御に使用されるシステム。
- PID(Proportion-Integral-Derivative):温度、流量、圧力、速度を調整する産業用制御機器に使用される機器。
- DCS(Distributed Control System):工場、機械、または制御エリア全体に地理的に分散した制御ループを使用するデジタル自動産業制御システム。
このレベルは監視レベルと呼ばれていて、前のレベルがPLCを利用するのに対し、このレベルではSCADAを利用します。SCADAとは、Supervisory Control and Data Acquisitionの略で、日本語では「監視制御・データ収集」と訳されます。
レベル3:プランニングレベル / 運用管理
このレベルでは、MES(製造実行システム)と呼ばれるコンピュータ管理システムを利用します。MESは、工場やプラントにおける原材料から完成品までの製造プロセス全体を監視します。
レベル4 : 企業レベル(ビジネスプランニングとロジスティクス)/ 戦略
ピラミッドの頂点は、経営レベルと呼ばれるものです。このレベルでは、ERPとして知られている企業の統合管理システムを使用しています。
第4次産業革命(インダストリー4.0)とは
産業世代
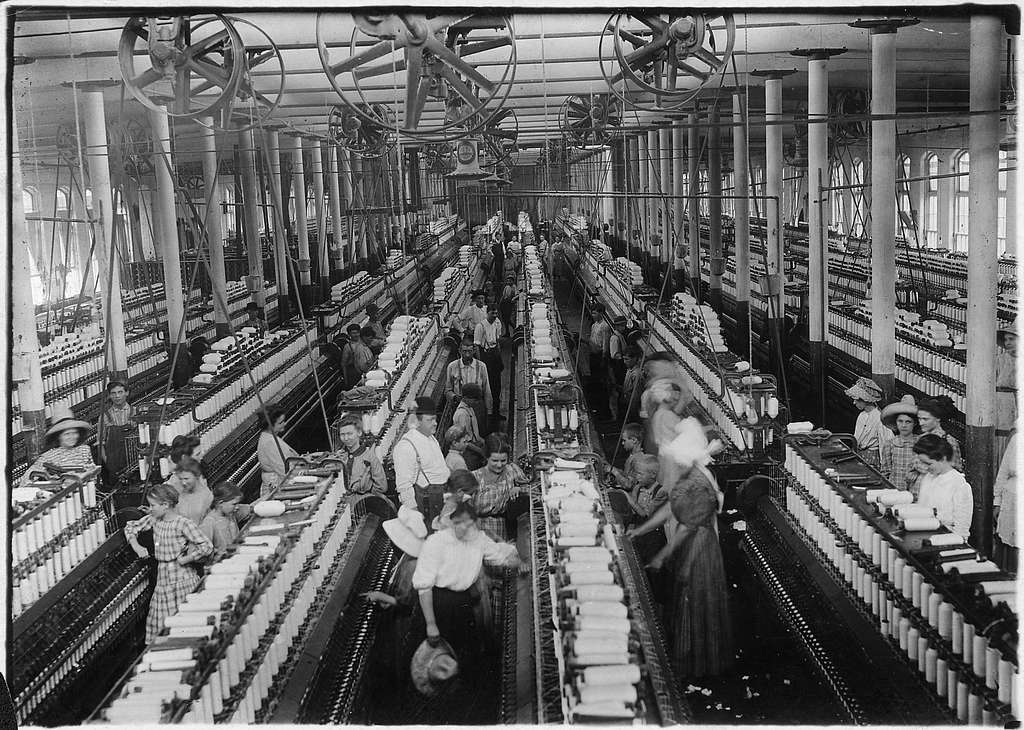
第一次産業革命
18世紀後半にイギリスで始まった第一次産業革命は、従来の人や動物の動力源から、水力や蒸気を動力とすることで大量生産を可能にしました。それまで手作業で行っていた完成品の製造を、機械で行うようになりました。

Photo on Flickr Run-A-Bout | Assembly line at Kalamazoo Manufacturing Compan… | Flickr
第二次産業革命
100年後、第二次産業革命が起こり、組み立てラインや石油、ガス、電気が使われるようになりました。これらの新しい動力源と、電話や電信による通信手段の発達により、製造工程に大量生産とある程度の自動化がもたらされました。
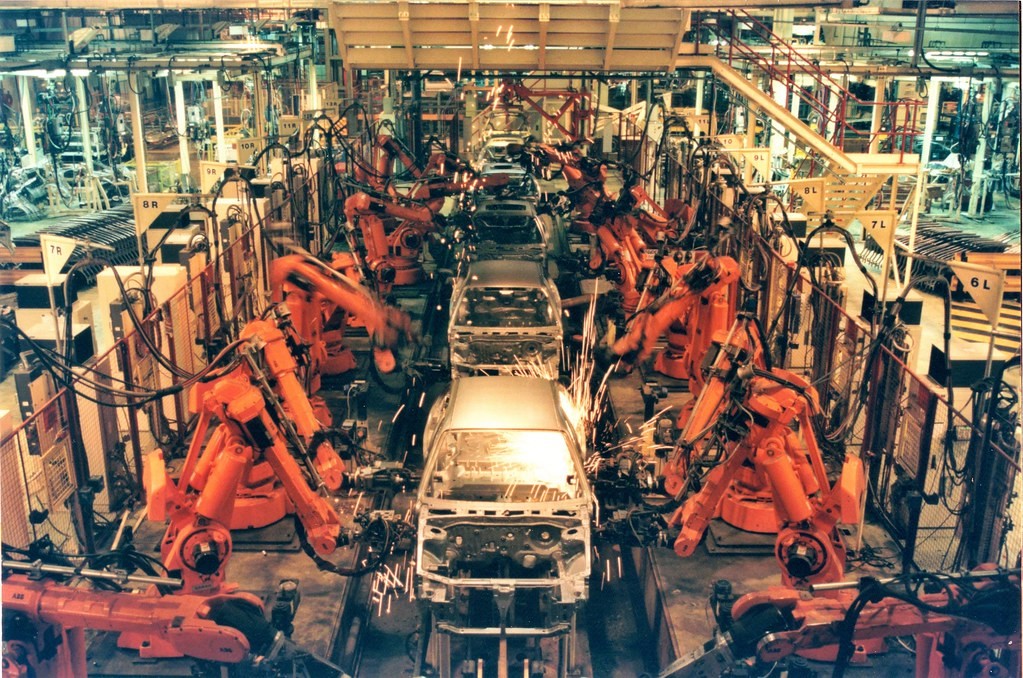
Photo on Flickr - rover 200 framing line | Flickr
第3次産業革命
20世紀半ばに始まった第3次産業革命では、製造工程にコンピューター、高度な通信技術、データ分析が加わりました。工場のデジタル化は、PLCを機械に組み込むことで一部の工程を自動化し、データを収集・共有することから始まりました。
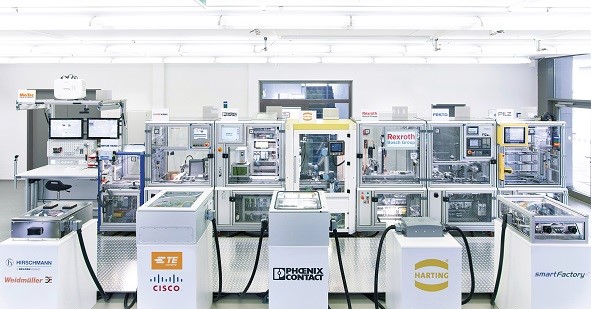
SmartFactoryKL Pressekontakt, CC BY-SA 4.0, via Wikimedia Commons
第4次産業革命
インダストリー4.0とも呼ばれる第4次産業革命の時代とは、自動化が進み、スマートマシンやスマートファクトリーが導入され、全体でより効率的かつ生産的に商品を生産することができるようになりました。柔軟性が向上し、メーカーはカスタマイゼーションによって顧客の要望に応えられるようになり、少数のオーダーでも効率よく生産できることが多くなりました。工場現場からより多くのデータを収集し、それを他の企業のオペレーションデータと組み合わせることで、スマートファクトリーは情報の透明性とより良い意思決定を実現することができます。
第4次産業企業
インダストリー3.0は大量生産へのスケーリングを導入しましたが、インダストリー4.0はカスタマイズ生産へのスケーリングを導入します。今後、私たちのニーズが多様化すればするほど、カスタムメイドの需要が高まります。
オートメーションピラミッド+インダストリー4.0
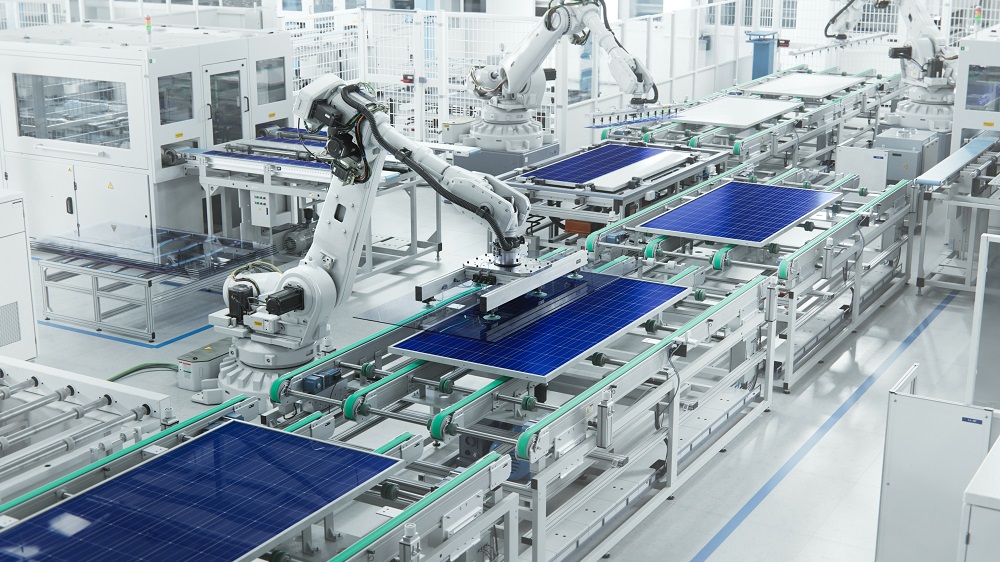
オートメーション・ピラミッドは、企業が製造業を効率的に管理するための優れた基準であり、組織内のコントロールを可能にするものでしたが、このモデルは完璧ではありませんでした。このモデルの弱点は、柔軟性に欠けることで、新しい製品を作るとなると、製造の流れをすべて構築することになります。そのため、新製品ができるまで何カ月もかかってしまい、製造や製品に問題が発生した場合には、修正・変更を加えてから再出荷するまでに時間がかかることもありました。
インダストリー4.0モデルでは、製造装置にインテリジェンスを加えることで、フィードバックに基づくオンタイムの変更や、機械学習による反復学習が可能になりました。インダストリー4.0は、ピラミッド型モデルを置き換えるものではありませんが、信頼性を損なうことなく、その欠点をすべて改善したモデルです。
可視性の向上
よりスマートなセンサーを追加することで、稼働中のロボットや機械が受け取ることができる情報量が増加します。もちろん、その状態だけでなく、機械の摩耗や劣化についても洞察できるようになりました。メンテナンスが必要だと判断した場合には、自動でアラートを出すことも可能です。これらの情報をもとに、ネットワークを通じて工場の現場をリアルタイムに見ることができる仮想環境「デジタルツイン環境」を構築することも可能になったのです。
機械学習
工場の設備や機器をクラウドに接続する企業が増えています。これらの情報を分析し、機械学習モデルを構築し、繰り返し学習させることで、生産性の向上や効率化を図ることができます。
コミュニケーションの向上
工場の設備や機器をインターネットに接続することで、サプライヤーや顧客とのリアルタイムなコミュニケーションが可能になり、効率性が向上します。サプライヤーは、必要な時にだけ工場に納品もしくは引取りに行くことができます。また、共同作業者は、現在の情報に基づいて計画を立てることができ、お客様に対しても、作っている製品についてより高い透明性を提供することができます。
ジャストインタイム生産
工場はインターネットに接続されているため、お客様はいつでも必要な時に製造工程に手を加えることができます。また、フィードバックにより変更が必要な場合でも、大きな損失が出る前に変更することができます。
これは、古典的なオートメーション・ピラミッドから、より近代的な工場へのインダストリートランスフォーメーション(IX)につながっていきました。
インダストリー・トランスフォーメーション(IX)
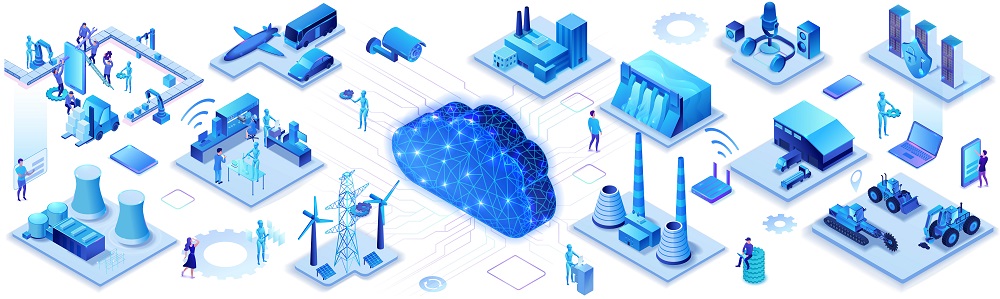
IXというコンセプトは新しいものではない。電気やセンサーといった技術的なものから、Ford社のアセンブリ―ラインのような組織的なものまで、過去にたくさんありました。インダストリー4.0のIXは、もう一つの変革トレンドであるデジタルトランスフォーメーション(DX)と密接に結びついていて、この変化には、技術的な変化と組織的な変化の両方が伴います。
IX+DX
このようにワークフローを分離することで、ITチームが工場の状況を見るためにアウトソーシングすることも可能になります。また、ロボットや機械も、内部に計算能力を追加することで、より良く、より速くカスタマイズできるように変更する必要があります。多くの企業は、ロボットアームや製造工程を、さまざまな工程をこなせるようにし、柔軟に役割を分担できるようにしているのです。
IXの課題
新世代の工場を実現するのは簡単なことではありません。新しい技術を導入しても、その効果が発揮されるまでにはまだ時間がかかるでしょう。マッキンゼーによれば、最も困難なのは、考え方を変えることだといわれています。企業にとって、自分たちのプロセスが他の人たちと共有されることを受け入れるのは非常に難しいことなのです。以下に、その難題のいくつかを紹介します。
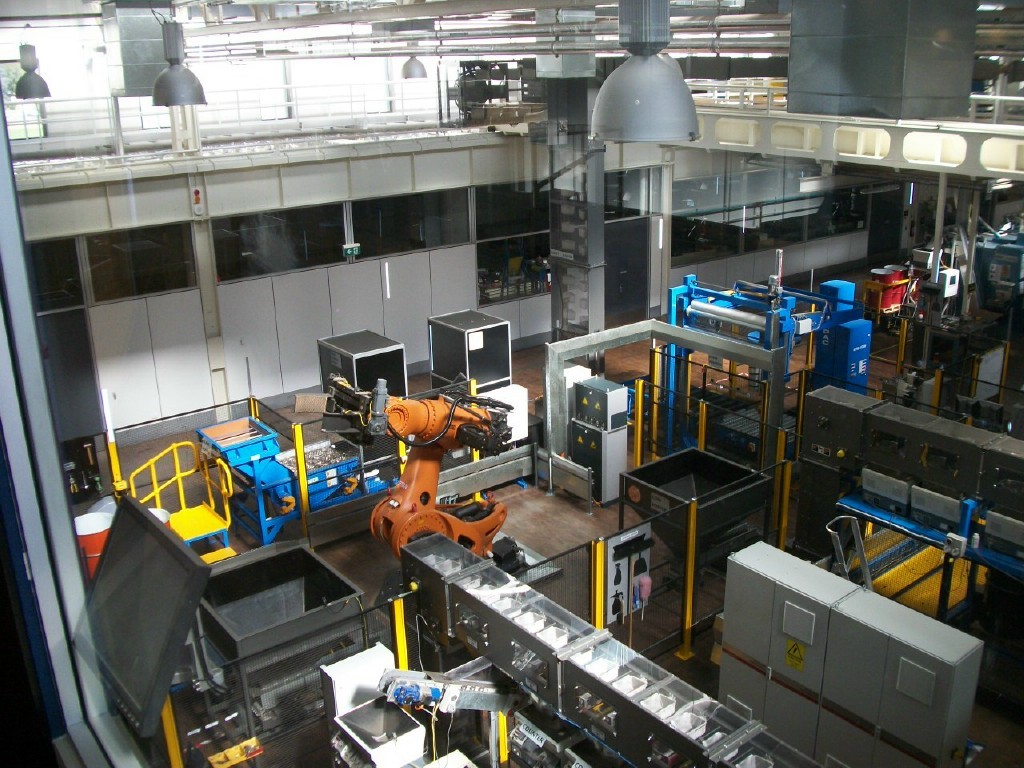
- 技術的スキルのギャップ:人材に求められるニーズは進化しています。製造工程とそれを支えるデジタルツールの両方を理解する人材が必要です。両方を熟知して、新たなビジネスモデルを作れる人は少ないため、トレーニングが必要になるかもしれません。
- データの機密性:テクノロジーの進化は、データおよびIPのプライバシー、所有権、管理に関する懸念の増大をもたらしました。AIアルゴリズムをうまく実装するためには、それを学習させ、テストするためのデータが必要です。そのためには、データを共有する必要があります。しかし、多くの企業は、サードパーティのソリューション開発者とデータを共有することに消極的です。
- 相互運用:もうひとつの重要な問題は、プロトコル、コンポーネント、製品、システム間の分離がなされていないことです。相互運用性は企業の技術革新の妨げになります。ベンダーを別のベンダーに、あるいはシステムのある部分を別のものに簡単に交換できないため、相互運用性はシステムコンポーネントのアップグレードの選択肢を制限することにもなります。
- セキュリティ:スマート・ファクトリーを構成する物理的およびデジタル的なシステムは、リアルタイムの相互運用性を可能にしますが、その反面、攻撃対象が拡大するリスクを伴います。スマート工場では、多数の機械やデバイスが単一または複数のネットワークに接続されているため、それらの機器のいずれかに脆弱性があると、システムが攻撃を受けやすくなる可能性があります。この問題に対処するために、企業は企業システムの脆弱性とマシンレベルの運用上の脆弱性の両方を予測する必要があります。 企業は、このようなセキュリティ上の脅威に対処するための準備を十分に整えておらず、多くの場合、脆弱性の有無を確認するためにテクノロジーやソリューションプロバイダーが必要です。
- データ増加への対応:より多くの企業がAI活用に依存するようになると、企業は、より多くのデータが生成されることに直面することになります。取得したデータをより有効に活用するためには、それを理解できる人がいることが重要になるでしょう。